Table of contents
Polyurethane spray foam is a great way to insulate your home. It is versatile in its usage and is highly effective in shielding homes and businesses from thermal penetration. As you know, they are divided into open-cell and closed-cell insulation. Both types are effective for wall cavity insulation purposes.
When contractors install spray foam insulation, it is a liquid, but it expands quickly, solidifying and creating bubbles. In the following paper, some main points for properly insulating with spray foams are reviewed.
The properties of spray-applied polyurethane thermal insulation may vary depending on such factors as the thickness of the foam sprayed, the temperature and type of substrate, the ambient temperature and humidity, the number of spray passes, and the output of the equipment. The properties may also vary depending on different manufacturer’s liquid components.
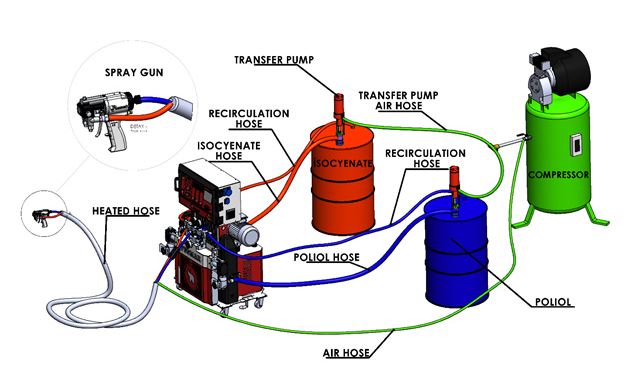
Appropriate thickness for sprayed polyurethane foam
R-Value is a measure of how well an object resists the flow of heat. Insulation is rated in R-Value per inch, which represents how effective each inch of thickness is. Prior to applying spray foam, optimized thickness is calculated. The actual thickness of foam is more dependent on the type of foam (closed-cell or open cell), formulation and temperature rise during the foaming process.
The thickness is perfectly controllable and can be modified by altering the application speed and/or mixing chamber of the gun. It is worth mentioning that the lower the number of layers applied to achieve a certain thickness, will achieve a higher density foam, achieving better density distribution and consequently, better thermal properties. When applying a very large thickness, the applicator must apply in thinner layers rather than one thick layer, and must allow time for the spray foam applied to cool between adding each layer to prevent high exothermic reactions, which would influence the quality of the foam. In other words, If the foam is sprayed thicker than recommended for its type, excessive heat can result causing odors, cracks, shrinkage, or charring. To spray more than one layer, apply in layers allowing the foam to cure for at least 15 minutes between layers.
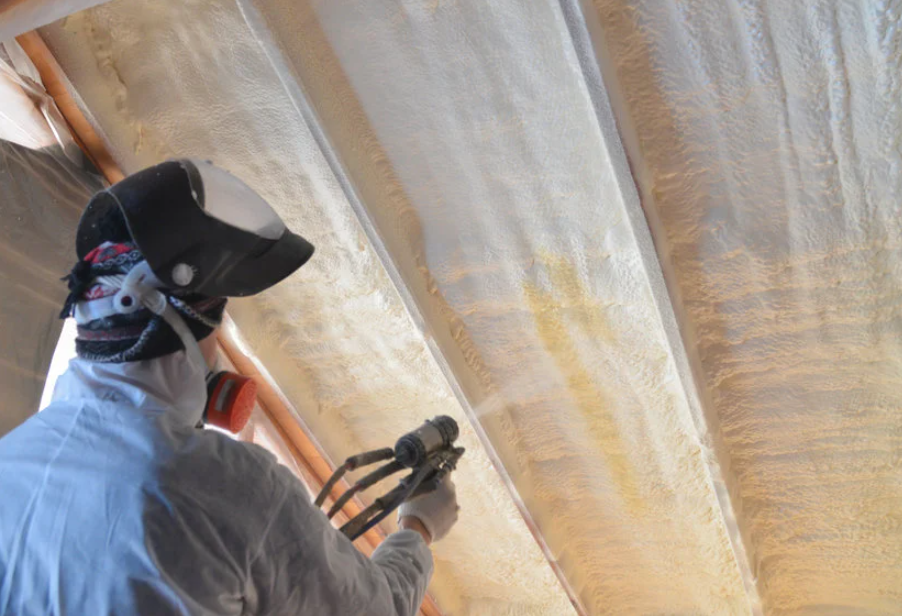
Optimized temperature before applying spray foam
Knowing the ambient temperature, substrate temperature, and temperature of your components is key to using spray foam insulation properly. The ideal temperature for both the foam and the surface is between 65° F and 90° F. Surfaces that are colder will result in reduced yield because the cold surface extracts heat from the exothermic reaction resulting in a reduced rise. If the surface is 40° or colder, the exotherm may also cause condensation, which would be like spraying foam onto a wet surface.
Surfaces that are too warm may result in the foam curing too fast. This would also result in a reduced yield because the foam would not have enough time to reach the full rise before a tack free state. In addition, extreme cases may result in loss of adhesion because the foam would cure so fast it could not develop a bond to the surface before it hardened.
UV protection for sprayed foam
Sprayed polyurethane foam applied in situ has an excellent behavior against atmospheric agents (water, extreme temperatures, wind, …). It is only attacked by long-term exposure to ultraviolet radiation, contained, for example, in direct sunlight. Although there is a layer of high density external skin, this attack causes the destruction of the polyurethane surface, resulting in a dusty appearance on the surface of the foam.
To avoid this action, exterior applications must be coated with specific materials such as polyurethane elastomers, polyurethanes, paints or any other specific coating for exterior use. These protections, like any other material, must be monitored for their conservation and maintenance. In the case of partially degraded foams, sanitizing must be carried out by means of a barbed brush or water under pressure and the subsequent application of a new layer of polyurethane foam and the suitable surface protection.
Prevention of cracking by expansion joints
In the polyurethane foam that is directly applied on expansion joints, cracks may occur due to the movement of the substrate by expansion or contraction. This effect can break the waterproofing property. It is easily avoidable if, at the time of the application, the proper precautions are taken by treating the joint properly.
Although polyurethane foam does admit some permanent deformation, the stresses generated by the effects of expansion-contraction on very wide joints, from 2 to 4 cm, cannot be absorbed by the foam. The way in which these stresses can be absorbed is to distribute them, minimizing their effects, by installing an elastic separating membrane, for example, made of synthetic rubber with a width of 30 cm, and applying polyurethane on top of it.
At last, it has to be reminded that one should hire professionals to install the insulation because it can be toxic and ineffective if the chemical makeup is incorrect.