Table of contents
Sandwich panels are one of the most economical insulation solutions, with greater durability, shorter installation time, less need for maintenance and greater capacity for acoustic and thermal insulation. In addition, they can be adapted to all building needs and typologies, with different types of panels for each case.
Types of panels according to the application
Sandwich panels for roofs
In this case, the panels are highly exposed to the action of rain, snow or wind, as well as to their weights. They are installed on roofs and decks of all types of buildings, although they are most commonly used on roofs with a minimum slope of 7%.
Their installation is usually combined with watertight joints, which makes installation quick and easy and does not reduce the insulation of the roof. Self-drilling screws are also used to fix them to the structure, and sealing systems are used to prevent water seepage.
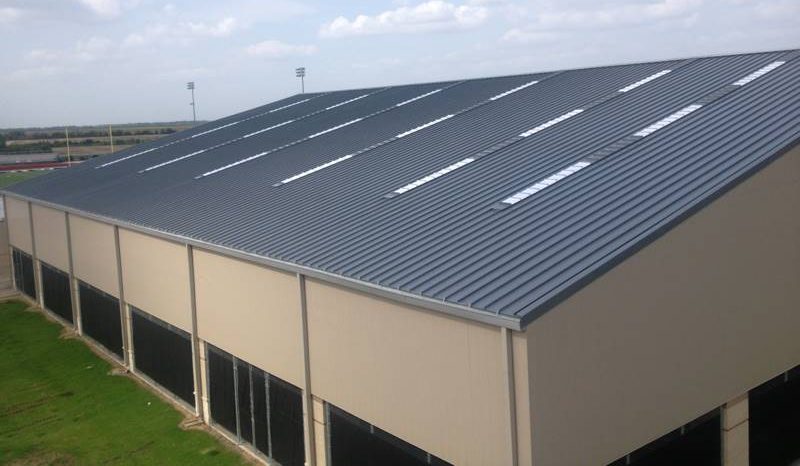
Sandwich panels for facades
The variety of finishes of sandwich panels make them a very popular choice for facades. They have the advantage that the final result is very aesthetic because the fixings are hidden. Other advantages are their lightness, modularity and high insulation performance.
This type of panels is mainly used to insulate facades and walls, as well as interior walls. They are suitable for industrial buildings, sports centers, residential and public buildings.
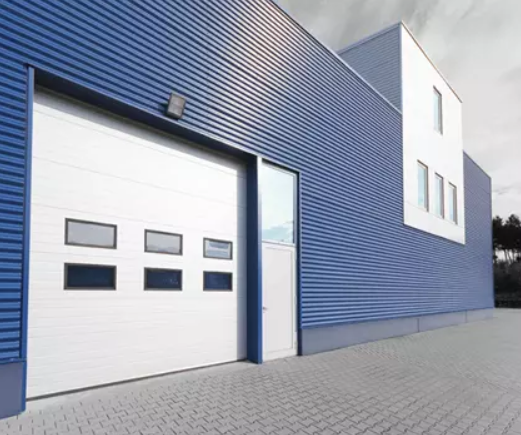
Refrigeration panels
The panels are also used to insulate temperature-controlled spaces, such as cold rooms or freezers. In fact, refrigeration, food safety and food waste are intimately related. Perishable foods should be kept refrigerated or frozen throughout the entire supply chain.
To allow transportation without damaging the merchandise, refrigeration or freezing temperatures have to be kept constant even when external temperatures vary markedly, so features such as a high insulation value and hygiene are just as critical as light weight, a high loading capacity and ease of unloading. Containers insulated with rigid polyurethane foam are used almost exclusively nowadays on account of the excellent properties of this material. Polyurethane is also being used more and more as a core material for sandwich panels for refrigerated vehicles. High mechanical strength, high insulating efficiency and economical production are combined in this core material. These properties have to be maintained throughout the service life of the product, which often exceeds 15 years.
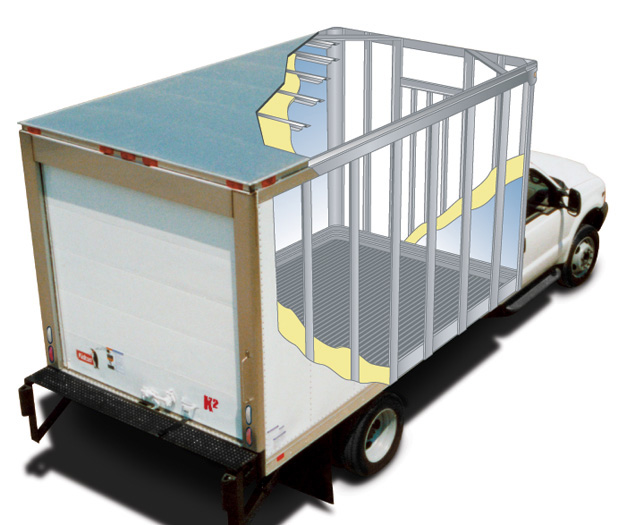
In the last paper, we talked about sandwich panel structures in roofs and facades; in the following paper, refrigerated trucks is going to be discussed.
Polyurethane for refrigerated trucks
The walls, floors, ceilings and doors of these trucks contain an insulating material that separates the interior temperature from that of the exterior. Polyurethane is a material widely used to achieve the necessary thermal stability. As a matter of fact, among different insulating materials (such as cellulose, mineral wool and fiberglass), PU has the lowest coefficient of thermal conductivity.
The panels are heat cured in the molds to form a rigid sandwich panel which has high strength and excellent insulation property. The material for sheet metal is galvanized steel which is pre painted and has layer of polythene on top. This gives the panel great insulation and is completely rust resistant properties.
Insulation properties are usually measured by R-Values. R- Value is a relationship between thickness of material and the transfer of heat per unit area. Consequently, for a correct installation of the insulating material, the most suitable thickness must be calculated. To do this, various factors must be taken into account, such as:
- The ideal internal temperature
- The type of products to be transported
- How many times the doors will be opened
- How the air will circulate
- The total weight of the products
- The loss of heat
- Density of the chosen material
Manufacturing process for refrigerated trucks
There are basically two methods of PU sandwich panel production process, namely continuous production and discontinuous production. The way of applying foaming material on the surface of metal parts can be done by:
- Injection of polyurethane
This method, is a process by which the metal sheets are filled with the insulating material. The discontinuous process is suitable for low production volume and it is an excellent insulating solution for refrigerated trucks. Unlike discontinuous production, the continuous process is suitable for enterprises with high output requirements; PU foam is continuously injected on the upper and lower surface materials that are formed at a uniform speed. After polymerization occurs there, and the sandwich panel is fully formed, the cutting is performed to the expected length.
To sum up, the significant growth in cold chain infrastructure is directly tied to a need for more refrigerated trucks on the road. Rigid polyurethane foam is an essential component for refrigerated truck bodies and used by leading manufacturers worldwide to make thermal efficiency and climate control possible. Polyurethane foam offers excellent insulation value that is superior to traditional materials.